Introduction
As a core component of precision circuit control, the contact gap is a key parameter in determining the performance of a micro switch, which directly affects the sensitivity, life span and environmental adaptability. With the increasing demand for miniaturization and high reliability in industrial automation and consumer electronics, the design and application of contact gap has become the focus of technological competition in the industry. This article will combine industry standards and innovative cases to analyze the technical characteristics and application logic of contact spacing.
Contact Pitch Types and Characteristics
The contact spacing of micro switches is usually divided into four categories, covering the whole range of scenarios from high-precision to high-vibration resistance, and the four types are 0.25mm class, 0.5mm class, 1.0mm class, and 1.8mm class, respectively. The sensitivity and shock resistance of microswitches are negatively correlated with the contact pitch; 0.25mm contact pitch has ultra-small pitch design and high sensitivity (action force ≤ 0.1N), but its shock and vibration resistance is weak. Usually used in medical equipment (such as surgical instrument keys), precision sensor triggering, etc., need to strictly control the current (≤ 0.1A) to reduce contact loss. The contact pitch of 0.55mm level is the common standard in the industry to balance the sensitivity and durability, and its mechanical life can reach more than 5 million times. Typically used in consumer electronics (mouse buttons), home appliance control (microwave oven door switches) and other low to medium current scenarios. 1.0mm contact spacing strengthens vibration resistance (shock resistance ≥ 50G) and supports breaking of currents above 10A, but with a slightly slower response speed. Usually used in industrial machinery limit switches, new energy vehicle charging pile emergency stop protection, etc. 1.8mm contact pitch has a large pitch design, arc resistance increased by 50%, suitable for frequent on-off high load scenarios. Often used in power system circuit breakers, heavy machinery (crane limit detection) and other extreme environments.
Technical Challenges and Innovative Directions
Although the reduction of contact pitch can improve sensitivity, it faces two major challenges: 1. Arc erosion: In high-current scenarios, the small pitch is prone to oxidization of contacts due to arc erosion, which shortens the life of the contact. The solution includes silver-nickel alloy contacts and ceramic interrupter design, which can extend the electrical life to more than 500,000 times. 2. Environmental tolerance: vibration and shock are prone to false triggering. Manufacturers have optimized reed preload spring force (e.g., Honeywell's V15 series) and damping structure to improve the vibration resistance of 1.0mm pitch switches by 40%.
Industry Application Trends
Intelligent upgrading: Micro switches with integrated pressure sensing chips (such as Tesla Optimus robot fingertip module) realize adaptive control by dynamically adjusting the pitch through real-time monitoring of contact status.
Green manufacturing: EU RoHS 3.0 promotes the popularization of cadmium-free contact materials, and 0.5mm pitch switches take the lead in adopting environmentally friendly silver alloy, taking into account both performance and compliance.
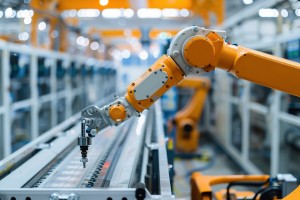
Conclusion
From the millimeter precision of medical equipment to the thousand pounds of heavy industry, the technological evolution of micro switch contact pitch reflects the manufacturing industry's ultimate pursuit of precision and reliability. In the future, with the integration of material science and intelligent algorithms, this “microscopic parameter” will continue to empower the upgrade of the global industrial chain.
Post time: Apr-08-2025